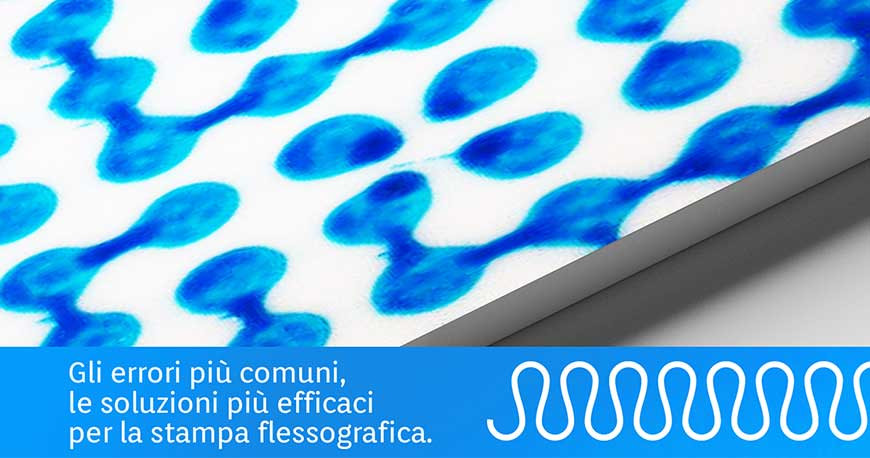
Stampa flessografica: 12 comuni errori e loro soluzioni!
Stampa flessografica: 12 comuni errori e loro soluzioni!
Stampa flessografica, ecco le soluzioni più efficaci per rimediare agli errori più comuni che si possono riscontrare nelle varie fasi della stampa per packaging.
Di seguito, ulteriori errori più comuni, dei 24 totali che abbiamo già trattato nell’articolo precedente, da verificare e rimediare seguendo i suggerimenti. Nella terminologia tecnica è molto ricorrente la versione anglosassone che riportiamo tra parentesi, visto l’origine americana del settore.
Questi sono i dodici errori, e rimedi, che si possono riscontrare nella stampa flessografica:
- L’INCHIOSTRO ASCIUGA TROPPO LENTAMENTE (INK DRYING TOO SLOWLY)
- L’INCHIOSTRO ASCIUGA TROPPO RAPIDAMENTE (INK DRYING TOO QUICKLY)
- FUORI REGISTRO (MISREGISTER)
- EFFETTO MOIRÈ (MOIRÈ EFFECT)
- STAMPA MACULATA (MOTTLED PRINT)
- PUNTI BIANCHI (PIN HOLING)
- MANCANZE (SKIP OUT)
- BARRATURE (STRIKETHROUGH)
- ALONATURE (HALOS)
- EFFETTO PONTE (BRIDGING EFFECT)
- RIFIUTO DEL COLORE (TRAPPING)
- PUNTI VUOTI AL CENTRO (EMPTY POINTS)
L’INCHIOSTRO ASCIUGA TROPPO LENTAMENTE (INK DRYING TOO SLOWLY). |
|
Questo fenomeno avviene quando un colore si mescola in modo inaspettato con un altro. Oppure quando i colori non si sovrappongono correttamente (trapping). L’inchiostro si stacca dal supporto oppure si trasferisce su altri rulli del sistema di stampa. Può verificarsi che la stampa si incolla nelle bobine. |
|
CAUSE |
RIMEDI |
Il primo colore stampato asciuga troppo lentamente oppure il colore che si sovrappone al primo asciuga troppo velocemente. |
Regolare la velocità di asciugamento e/o la viscosità del primo colore stampato, al valore più basso possibile. Regolare la viscosità del secondo colore ad un valore leggermente più elevato. Regolare la pressione della lastra al minimo necessario per ottenere una buona qualità di stampa. |
L’inchiostro in uso ha una viscosità eccessiva oppure il rullo anilox non è quello giusto. |
Controllare la viscosità dell’inchiostro. Controllare le specifiche dei rulli anilox. Controllare la racla e/o la pressione del rullo inchiostratore. |
Asciugamento insufficiente oppure sbilanciato. |
L’essiccatore deve essere in grado di adattarsi alla velocità, gli essiccatori tra gli elementi di stampa devono essere bilanciati. |
Temperatura della sala stampa basso e/o umidità troppo elevate. |
Regolare le condizioni ambientali della stampa a quelle ideali. |
Velocità di stampa eccessiva. |
Ridurre la velocità di stampa. |
Bilanciamento dei solventi non corretto. |
Controllare che la viscosità dell’inchiostro sia adeguata al tipo di lavoro. Inchiostro di quadricromia caricato per errore in un gruppo stampa con anilox senza racla (con rullo dosatore). |
PRO TIP
I cliché flexo forniti da Flexo 24 rispettano le avvertenze della casa madre produttrice del fotopolimero. Leggere attentamente le avvertenze e soprattutto la compatibilità degli inchiostri con solventi.
L’INCHIOSTRO ASCIUGA TROPPO RAPIDAMENTE (INK DRYING TOO QUICKLY). |
|
Quando l’inchiostro asciuga sulle lastre, ovvero sui cliché, e anche sui rulli, e quindi non si trasferisce sul supporto. Non è rato che questo difetto si riveli sul bordo anteriore del supporto. |
|
CAUSE |
RIMEDI |
Il valore pH è basso, verso il valore basico, non acido, dovuto alla perdita di ammine. |
Aggiungere all'inchiostro uno stabilizzatore di pH. |
Viscosità fuori controllo. |
Mantenere la viscosità di stampa corretta. Non stampare a viscosità elevate. |
Correnti d’aria sull’unità di stampa. |
Tenere distante dalle unità di stampa qualsiasi ventilazione diretta. Evitare correnti d’aria provenienti da porte, finestre e ventilatori. Controllare la soffieria degli essiccatori tra le unità. |
Bilanciamento dei solventi non corretto. |
Usare la miscela corretta di solventi, solventi deboli tendono a far precipitare i componenti dell’inchiostro. |
Trasferimento dell’inchiostro insufficiente. |
Usare un anilox con volume corretto. Non usare una viscosità troppo bassa. |
Temperatura della bobina troppo elevata all’ingresso nella unità di stampa. |
Ridurre la temperature di preriscaldamento all’ingresso della unità di stampa. |
La sala stampa con temperatura elevata e/o umidità troppo bassa. |
Ottimizzare le condizioni termoigrometriche dell’ambiente attorno alla macchina. |
Con la newsletter di Flexo 24 ricevi subito € 20,00 di sconto per il primo ordine superiore a € 199,00, e solo info utili. Iscriviti:
FUORI REGISTRO (MISREGISTER). |
|
È un errore che può verificarsi in tutti i sistemi di stampa, anche nella stampa flessografica. Esso si presenta quando i colori che compongono testo o illustrazioni non si sovrappongono perfettamente. Per controllare accuratamente e in tempo reale la stampa sul supporto, Flexo 24 mette a disposizione il Lentino digitale, adatto per la maggior parte degli smart phone, ha un potere di ingrandimento 30x. |
|
CAUSE |
RIMEDI |
Le lastre, i cliché, non sono montati a registro. |
Rimontare le lastre a registro. Rivedere le procedure di montaggio-lastre e di preparazione. Controllare lo spessore delle lastre, la distorsione e l’altezza del rilievo. Controllare lo spessore del biadesivo. |
Tensione del nastro del supporto non corretta. |
Regolare il dispositivo di controllo della tensione in funzione del supporto da stampare. |
Regolazione errata dei rulli guida. |
Verificare il parallelismo tra i rulli guida per assicurare, la pressione deve essere uniforme su tutta la larghezza nastro. |
Eccessiva temperatura della bobina. |
Ridurre la temperature di asciugamento. |
Compensatori di registro della macchina fuori centratura. |
Centrare i compensatori di registro laterale e longitudinale prima di regolare manualmente il registro del lavoro. |
I rulli a folle o in rotazione libera frenano o girano ad intermittenza. |
Sostituire o lubrificare i supporti dei rulli a folle o in rotazione libera. |
La macchina è fuori allineamento. |
Riallineare la macchina. |
EFFETTO MOIRÉ, O MAREZZATURA. (MOIRÉ EFFECT). |
|
Si verifica come una interferenza ottica indesiderata per un dis-allineamento tra gli angoli del retino dei diversi elementi di stampa. Per controllare la lineatura di stampa mettiamo a disposizione una pellicola fotografica in acetato trasparente: il contalinee flexo, con il quale si può determinare la lineatura di stampa da un'analisi ottica immediata tra le linee e il retino della stampa in esame. |
|
CAUSE |
RIMEDI |
Angoli di retinatura errati. |
La differenza tra gli angoli di retinatura tra i diversi colori dovrebbe essere di 30°. Il giallo dovrebbe a 15° rispetto a Cyan e Nero. |
Il valore della lineatura dell’anilox è troppo simile a quella delle lastre, o valori multipli. |
L’angolo di retinatura delle lastre deve risultare a 7,5° rispetto all’angolo di retinatura dell’anilox. Selezionare un angolo di retinatura dell’anilox con un rapporto di almeno 5,5 a 1 rispetto a quello delle lastre, cioè, ad esempio, per lastre a 40 lcm scegliere un anilox a 220 lcm. |
PRO TIP
Come da indicazioni dello standard ISO 12647-6:2012 per la flessografia: la differenza nominale tra gli angoli dell'asse principale dei retini dei canali/colori Ciano, Magenta e Nero è di 30°. Mentre la differenza è di 15° per l’angolo del Giallo. Nessun colore dovrà essere allineato con l'angolo di incisione dell’anilox. Questo un esempio che può causare moiré: anilox a 65 lcm utilizzato per una lastra a 33 lcm perché 33 x 2 = 66 è troppo vicino a 65 lcm dell'anilox.
STAMPA MACULATA (MOTTLED PRINT). |
|
La stampa maculata, in inglese “mottled print”, si presenta come ampie zone stampate in modo non uniforme e non continuo dei fondini retinati e dei fondini pieni. È simile all'errore tipo schiuma (foaming), trattato nell'altro articolo dei primi decidi errori della stampa flessografica. |
|
CAUSE |
RIMEDI |
Superficie non uniforme della lastra, del cliché. |
Aumentare la pressione tra lastra e supporto di stampa. Aumentare la viscosità dell’inchiostro. Aumentare lo spessore dello strato di inchiostro. Usare una lastra più morbida. |
Inchiostro poco concentrato oppure con viscosità troppo bassa. |
Aggiungere inchiostro fresco o un prodotto adatto per correggere la viscosità per ottenere un grado di opacità maggiore. |
Cilindro di stampa sporco o con scalfitture. |
I rulli di stampa devono essere puliti accuratamente da inchiostro o altri materiali estranei. |
Superficie non uniforme della lastra e ricettivo. |
Usare lastre più morbide o comprimibili oppure biadesivo più comprimibile. Verificare la validità del trattamento superficiale del supporto. |
L’inchiostro non si stende sul supporto (non bagna il supporto). |
Assicurarsi che il bilanciamento dei solventi sia corretto. Cambiare il sistema di inchiostrazione. |
Tracce del processo di formatura rimaste sulla lastra. |
Lavare la lastra accuratamente con un prodotto compatibile. Rifare la lastra. |
PRO TIP
Per testare nuovi prodotti consigliamo di procedere con il TEST DI CALIBRAZIONE utile anche per impostare la curva di compensazione per l’aumento del punto stampa (dot gain stampa).
PUNTI BIANCHI (PIN HOLING).
|
|
È un fenomeno che si presenta quanto l’inchiostro usato per la stampa flessografica non riesce a coprire in modo completo e uniforme il supporto perché si formano in modo casuale delle zone non coperte dall'inchiostro nell’area stampata. I prodotti Flexo 24 sono garantiti per determinati tipi di inchiostri, consultare sempre le avvertenze prima dell'acquisto. |
|
CAUSE |
RIMEDI |
L’inchiostro asciuga sull’anilox e ha difficoltà nel trasferirsi sulla lastra. |
Usare solventi ad evaporazione più lenta. Diminuire la potenza degli essiccatori. Aumentare la velocità di stampa. |
L’inchiostro non forma uno strato uniforme sul supporto. |
Ridurre la viscosità dell’inchiostro. Aumentare lo spessore dello strato d’inchiostro. Aumentare la pressione della lastra sul supporto. Controllare il pre-trattamento del supporto oppure la sua superficie che può risultare irregolare o butterata. Controllare il sistema di inchiostrazione. |
Anilox consumati. |
Esaminare le condizioni degli anilox e sostituirli se necessario. |
Sporco sul cilindro di stampa. |
Pulire il cilindro di stampa. |
Supporto non uniforme oppure non ricettivo. |
Usare cliché più morbidi oppure biadesivo più comprimibile. Verificare la validità del trattamento superficiale del supporto. |
MANCANZE (SKIP OUT). |
|
Questo errore si verifica per insufficienza o mancanza di trasferimento dell’inchiostro sul supporto, in modo parziale o totale. |
|
CAUSE |
RIMEDI |
Lastra con aree più basse, parti non incise. |
Verificare eventuali variazioni di spessore delle lastre. |
Realizzazione scadente dei cliché o di qualità scadente. |
Controllare le pressioni per determinare l’accuratezza di preparazione delle lastre. |
Pressione di stampa insufficiente. |
Reimpostare le pressioni dei cliché e/o degli anilox. |
Difetto di bloccaggio del gruppo di stampa. |
Controllare i dadi di bloccaggio del gruppo di stampa. |
Sbilanciamento del cilindro portalastre. |
Controllare l’eccentricità dei cilindri lastra, degli ingranaggi. Verificare lo stato di pulizia e di logoramento di alberi, perni, cuscinetti e ingranaggi. |
Elemento di stampa fuori parallelismo. |
Regolare l’unità di stampa per il parallelismo laterale. |
La superficie della lastra non si inchiostra. Trattamento superficiale della lastra non corretto. |
Pulire bene la lastra con solvente adatto. Sostituire il cliché. |
BARRATURE (STRIKETHROUGH). |
|
Sulla stampa risultano delle "barre", delle fasce rettangolari più scure, non volute; forme più o meno estese, irregolari oppure con cadenza regolare. |
|
CAUSE |
RIMEDI |
Eccentricità degli elementi rotanti fuori tolleranza (TIR). |
Verificare e, se necessario, correggere l’eccentricità del carrier (cilindri e maniche) e dei rulli anilox come da specifiche. |
Ingranaggi danneggiati, logori o sporchi. |
Verificare la condizione degli ingranaggi. |
Racla: troppo sottile o di qualità scadente. |
Usare una racla più spessa. |
Fluttuazione del supporto |
Regolare la tensione della banda del supporto. |
Verificare le caratteristiche delle lastre e del biadesivo |
Adattare lastre e biadesivo alle caratteristiche della macchina. |
Pressione troppo elevata tra l’anilox e lastra, che può causare vibrazione nel sistema di ingranaggi. |
Verificare e regolare la pressione di stampa tra anilox e lastra. |
Eccessiva pressione dell’inchiostro nella zona delle racle con pulsazioni che influenzano l’inchiostrazione dell’anilox. |
Monitorare il flusso di inchiostro. Se la pompa si sovraccarica probabilmente è insufficiente la sua portanza. |
Uso di cliché che non coprono l'intera rotaia del cilindro ma "a zona" dovuto all’impostazione grafica. |
Se possibile rivedere la progettazione grafica. |
La macchina da stampa presenta vibrazioni che si riportano sullo stampato. |
Modificare la velocità della macchina (le vibrazioni si possono presentare solo ad alcune velocità). |
ALONATURE (HALOS).
|
|
La grafica stampata, testi o retini, appaiono circondati da una linea o barra irregolare, non voluta che ne modifica le dimensioni. |
|
CAUSE |
RIMEDI |
Pressione di stampa non uniforme. |
Se l'eccentricità del carrier o sleeve, detta "TIR", è fuori specifica, controllare i valori e correggerli. |
Eccessiva inchiostrazione. |
Usare anilox con volume inferiore. |
Eccessiva durezza della lastra. |
Usare cliché più morbida e verificare il biadesivo. |
PRO TIP
La durezza del cliché, della lastra di stampa, è misurata in gradi shore: °shore. Con Flexo 24 è possibile ordinare cliché per la stampa flessografica da 1.14 mm, con durezza circa dai 74 ai 77° shore, fino a 5.50 mm con durezza di 33° shore. Contattare il supporto clienti per maggiori informazioni.
EFFETTO PONTE (BRIDGING EFFECT).
|
|
Ad una analisi accurata, la stampa non appare come da progetto grafico, perché i punti del retino, normalmente ben separati, si uniscono in modo irregolare. Per poter controllare visivamente la stampa consigliamo di acquistare il lentino digitale, adatto per la maggior parte di smart phone. |
|
CAUSE |
RIMEDI |
Volume degli anilox troppo elevato. |
Controllare e ridurre il volume degli anilox. |
Lineatura delle lastre toppo elevata rispetto a quella degli anilox. |
Verificare e normalizzare il rapporto delle lineature tra anilox e cliché. |
Eccessiva viscosità dell’inchiostro oppure inchiostro non adatto alla stampa di retinati. |
Correggere la viscosità dell’inchiostro oppure cambiare il tipo di inchiostro. |
Sporco sulle lastre da spolverio della carta. |
Pulire le lastre e verificare le condizioni della carta. |
Pressione di stampa eccessivo. |
Regolare la pressione. |
RIFIUTO DEL COLORE (TRAPPING).
|
|
Copertura del pieno irregolare nella stampa dei colori successivi al primo che risultano come parzialmente rifiutati. Si può verificare anche come rifiuto del colore dal parte del supporto stesso. Il valore di trapping può essere misurato con il densitometro. |
|
CAUSE |
RIMEDI |
Insufficiente asciugamento del colore stampato sull’elemento precedente. |
Ridurre le strato di inchiostro, aumentare il grado di essiccazione tra gli elementi. |
La somma dei colori stampati sovrapposti risulta eccessivamente elevata in termini di densità di inchiostro. |
Verificare la correttezza della riproduzione ed usare un valore di "Total Ink" o "Total Area Coverage" inferiore ed adeguato al sistema di stampa. |
Viscosità del secondo colore troppo bassa oppure tiro troppo elevato. |
Regolare la viscosità e il tiro degli inchiostri secondo la sequenza di stampa. |
PUNTI VUOTI AL CENTRO (EMPTY POINTS).
|
|
I punti stampati del retino appaiono nel risultato complessivo della stampa flessografica, come dei cerchi deformati a seconda della concomitanza di "fenomeni di slur". |
|
CAUSE |
RIMEDI |
Pressione di stampa eccessiva. |
Ridurre la pressione di stampa a valori normali. |
Lastra troppo dura e/o biadesivo troppo rigido. |
Usare lastre più morbide e biadesivo adatto. |
Tiro eccessivo degli inchiostri. |
Verificare e regolare il tiro degli inchiostri con aggiunta di solventi adatti. |
Viscosità degli inchiostri troppo bassa. |
Regolare la viscosità a valori normali. |
Acquista ora i tuoi cliché per la stampa flessografica con Flexo 24.